At Steaven Richard’s workshop, traditional forging techniques are seamlessly integrated with digital technology, resulting in the creation of one-of-a-kind masterpieces.
Located just a few kilometers away from Fontainebleau, Steaven Richard’s new workshop space is an expansive 1600 m2 hangar where he and his team have been settled for a year and a half now. This expansion was necessary due to the increasing number of orders, many of which were of gigantic proportions.
Originally trained as a blacksmith, Richard eventually turned his attention towards artistic ironwork and embarked on a ten-year journey across Europe before eventually settling in the heart of Paris in 2001. With the growing success of his business, the workshop doubled in size and became a company in 2011, receiving the prestigious Living Heritage Company label the same year.
The sound of the forge
Despite the size of the space, the workshop is filled with the sounds of machines and the smell of metal as fifteen employees, both men and women, work on various aspects of the production process, from metalworking to engineering. They all wear protective gear such as helmets, masks, and earplugs. As the company’s director, Steaven Richard ensures the smooth operation of the workshop and the quality of its creations. Although the team still uses traditional forging tools, Steaven Richard has developed a new technique called artistic rolling.
“Explore new aesthetic fields”
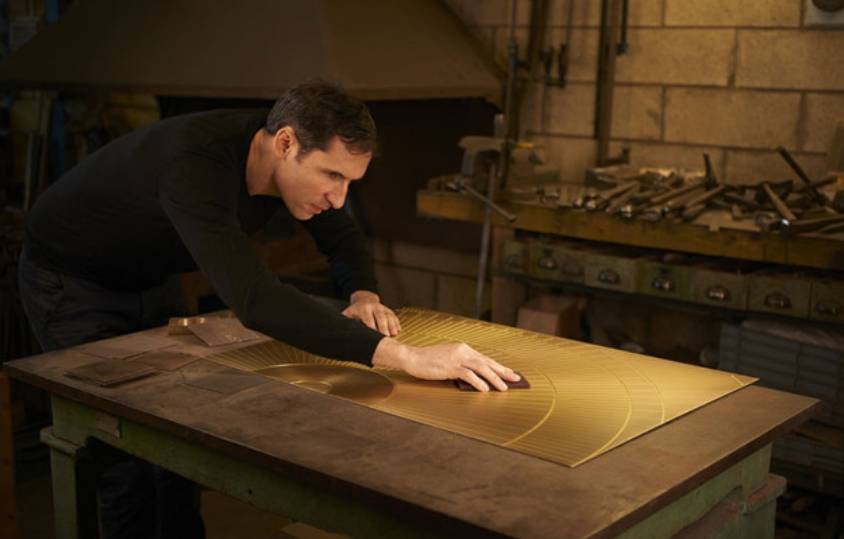
The process of artistic rolling involves creating textured patterns on sheet metals such as brass, copper, nickel silver (an alloy of copper, zinc, nickel, and occasionally lead in small amounts), and zinc. This method was developed by Steaven Richard in 2013 after working on a project for the Karl Lagerfeld studio at Chanel. The project involved creating a textured nickel silver metal floor with patterns similar to the Versailles parquet. Richard realized that the rolling mill used to texture the sheets could be used to explore new aesthetic possibilities with unique finishes. The rolling mill offers the advantage of creating distinctive textures on larger surfaces, which allows for endless creative possibilities in terms of patterns, rhythm, and material. After three years of research in collaboration with engineers, the technique was patented in 2018.
Endless creative possibilities

To begin the process, the sheets are passed through a rolling mill, which creates the desired texture. From these textured sheets, the metal is shaped using a digital milling machine to achieve custom profiles. Next, they create patinas in a range of colors and finishes through two methods: a cold process for bronze medals, or a hot torch process for various oxidation colors. A protective varnish is then applied to stabilize the piece. Finally, the assembly stage takes place either in the workshop or on-site.
Steaven Richard’s workshop produces one-of-a-kind large-scale pieces for individuals, hotels, museums, and major luxury brands. Their combination of traditional and innovative techniques has gained them increasing popularity, and the new workshop space is crucial in meeting the demand for their work.