Manufacturers utilizing milling processes may find themselves intrigued by the precision and efficiency offered by waterjet machining.
These machines excel at cutting intricate shapes in various metals, as well as nonmetals. What sets this technology apart is its unique ability to preserve the base metal’s properties during the cutting process, unlike thermal cutting processes that can introduce a heat-affected zone and alter the metal’s microstructure, leading to unwanted variability, particularly in precision-driven sectors like aerospace manufacturing. Waterjets, being a cold cutting process, offer a solution that eliminates such concerns.
However, the waterjet’s capabilities extend well beyond 2D sheet metal, plate, and tubular cutting. It possesses metalworking functionalities that are matched only by sophisticated devices like electrical discharge machines (EDMs) and mills.
When people refer to waterjet cutting as “waterjet machining,” they are actually more accurate than commonly acknowledged within the manufacturing world. Waterjets perform material removal through a controlled yet accelerated erosion process. Although no chips are produced, it remains a subtractive method. Moreover, in certain cases, waterjet machining proves to be a significantly more efficient subtractive process compared to other conventional metalworking technologies.
Operational Speed
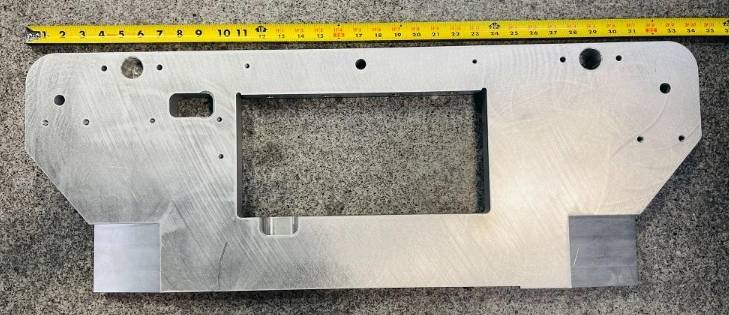
A waterjet machine excels at swiftly cutting geometry, often outpacing a CNC mill by a considerable margin. To illustrate this point, let’s take an example involving aluminum, specifically a 1.25-inch-thick motor mount plate crafted from 6061 T6 aluminum (refer to Figure 1).
The waterjet requires approximately 18 minutes to cut the entire plate. Considering an average tolerance for this fabrication process, the job setup takes approximately 15 minutes.
Using a traditional CNC mill to cut the same part takes around 30 minutes. The main challenge in this application arises from the need to flip the part to complete the job. As the part requires holding in vises, it must be taken out, flipped over, and then securely repositioned before the cutting tool can proceed with removing the excess material thickness that the vises initially gripped during the initial material removal.
Moreover, the setup time for this particular type of job is significantly longer compared to the setup for a waterjet cutting job. It typically takes approximately 2.5 hours to complete the setup.
The situation becomes even more intriguing if the same part is made from titanium, a material known for its challenging machinability. The low thermal conductivity of titanium leads to rapid temperature elevation in the work area, posing adverse effects on the cutting tools. Notably, as temperatures rise, titanium tends to become more malleable, referred to as “gummy” by some, and this can cause it to adhere to the tooling.
Considering all these factors, a 1.5-inch-thick motor mount plate made of titanium is processed on the waterjet in just 36 minutes. In contrast, the same part on a CNC mill requires a substantial 390 minutes to complete.
For any job shop, minimizing machine downtime is crucial since idle machines mean missed opportunities for revenue generation. This is where the waterjet truly stands out when compared to the mill, as its significantly faster processing times ensure more productive and profitable operations.
Typically, a shop can set up a waterjet for a job in just 15 minutes. Unlike other heavy and cumbersome devices, no complex loading procedures are required on the table. Instead, the workpiece can be easily placed on the slats of the table. Additionally, the process only requires a single cutting device, simplifying the setup further.
On the other hand, a machine shop may require approximately 2.5 hours for setup per job. The milling process involves using heavy and time-consuming workholding devices that must be installed before the cutting job begins. Moreover, multiple cutting tools are utilized for such milling tasks, each requiring loading into the machine and referencing to the workpiece.
Furthermore, due to its capability to work with large plates, a waterjet allows for nesting multiple parts on the same workpiece, comprising both similar and entirely different geometries. In contrast, CNC mills necessitate the use of a saw to cut material stock into blanks, and typically, the mill can only work on one piece at a time.
Metal Cutting Accuracy
When it comes to high-precision cutting, EDMs are unrivaled and widely favored in the tooling and moldmaking industry. The technology operates by removing material from a workpiece through a series of rapid recurring discharges between two electrodes. This method is particularly effective for creating intricate shapes in metal that would be challenging to achieve using conventional cutting tools.
The challenge with EDMs lies in their inherent slowness, which is the trade-off for their remarkable precision. However, smaller waterjet machines can offer accurate cuts with tolerances as tight as +/- 13 µm or +/- 0.0005 inches. While this may not match the level of precision achieved by EDMs, which some claim can reach tolerances of +/- 0.0002 inches (depending on the workpiece characteristics), it still falls within a range that is considered high-precision work by many.
Equipped with small nozzles and the capacity to deliver an exceptionally fine stream of water and abrasive, these high-precision machines excel at providing customer-specified cuts with minimal kerf. As a result, they are commonly employed in manufacturing environments that demand precision, including electronic companies, medical device manufacturers, and defense contractors.
Envision a medical multitool featuring minute teeth that, when set into vibration, can precisely cut through materials like bone. These teeth are so small that conventional milling methods are incapable of producing them, and EDM couldn’t meet the required speed for production. In such a scenario, the waterjet stepped in to deliver the necessary accuracy for the part within timeframes that proved highly appealing to the manufacturer.
Cutting Versatility
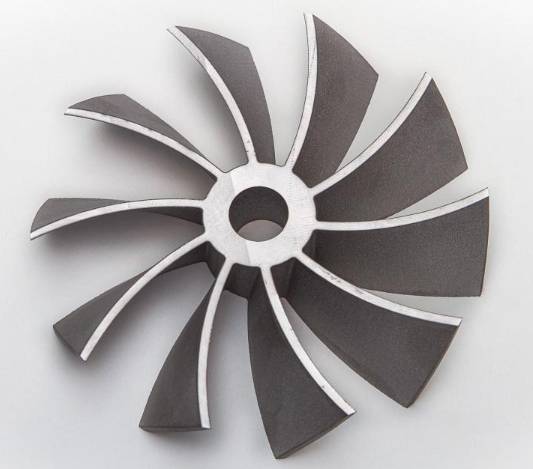
Describing a waterjet as a “Swiss Army knife” might seem like a stretch, but it truly possesses the versatility to perform various tasks typically associated with different types of metalworking machines (see Figure 2). For instance, it can cut intricate forms that would usually require a broach.
Nearly two centuries ago, broaching emerged as a technique for producing pulleys and gears. Today, it remains a widely used method in crafting high-precision gears for the automotive industry and manufacturing airplane components.
To utilize broaching in a shop, a broaching tool is essential. The broach operates by removing metal either as the workpiece moves against the stationary broach or as the broach is moved against the stationary object. This tool features teeth that vary in size and shape along its length, often with smaller rises per tooth at the beginning. Throughout the process, the broach performs roughing, semifinishing, and finishing passes to effectively remove metal from the workpiece.
Waterjets have the ability to replicate the cutting capabilities of a broach. They can perform the initial pierce, cut the circular shape in a single path, and then proceed with the finishing touches, adjusting the machine feed rate as required to achieve the precise finish necessary for completing the job.
Consider another example, such as the internal sharp corners that can be achieved on parts using a mill (see Figure 3). Starting with a 1-by-1-inch square of titanium, a CNC mill can only produce an internal radius as small as the smallest drill bit. However, at this point, the material removal process becomes slow and time-consuming.
A waterjet can achieve a cut with a 0.010-inch kerf, leading to an inside corner of the titanium square that resembles an internal feature created by a CNC mill. Moreover, waterjets excel at cutting nonmetals, like carbon fiber, in a much more efficient manner compared to CNC mills.
When working with carbon fiber, using conventional tools on a CNC mill is not recommended. Machining carbon fiber demands special tooling, higher spindle speeds than those used for metals, and lower feed rates than typical metal machining. These reduced feed rates help keep the heat low and prevent damaging the delicate carbon fiber material.
Waterjets possess the capability to pierce carbon fiber directly without the need for pre-drilling a hole. However, in certain instances where low-adhesion-level material or basic carbon fiber structures are used, starting the hole may require a 0.0625-inch-diameter drill. This is because using a jet stream of water and abrasive to pierce this cheaper carbon fiber material can lead to water seeping in between its multiple layers, potentially causing delamination. In such cases, the drill is placed next to the waterjet nozzle. Once the hole is made, the waterjet can begin cutting the carbon fiber.
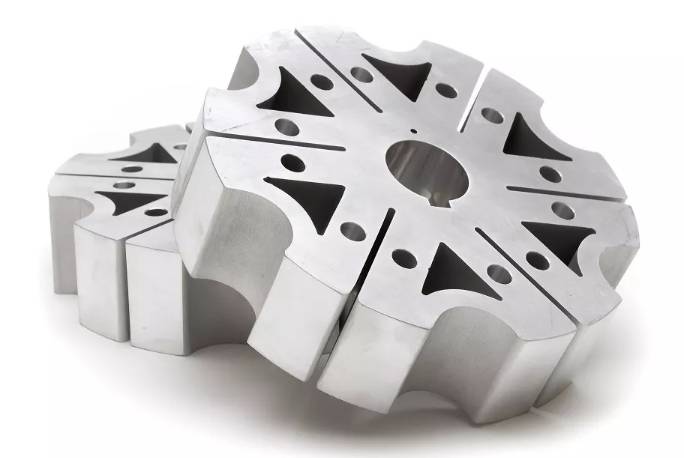
A Fabricator’s Machining Friend
Metal fabricating shops rarely venture into metalworking services purely by seeking such work. Instead, they often receive requests from customers, prompting them to acquire mills and lathes for their facility.
For those shops that prefer not to become full-fledged machining operations, a waterjet serves as a versatile cutting tool capable of providing numerous cutting capabilities comparable to a mill. The key lies in comprehending the waterjet’s potential and effectively harnessing its capabilities to meet customer demands.