Reports indicate that global steel production has experienced exponential growth over the past 70 years, with projections suggesting even higher levels in the future.
This is attributed to factors such as population growth, globalization, extensive infrastructure projects, increased manufacturing, a complex supply chain, and the growing demands across various sectors. Steel and its products hold immense significance in global trade and serve as vital contributors to the economic progress of nations.
Transportation of Raw Steel
Following the extraction of hot steel from blast furnaces, the steel undergoes a cold-hardening process and undergoes additional processing to enhance its strength, quality, and various surface and internal material properties. Subsequently, the steel is shaped and molded into various forms such as slabs, ingots, sheets, billets, and more, in a process commonly referred to as steel casting.
The processed bulk steel, in its various forms, is transported to a steel mill or another production facility, where it is transformed into commercial standard plates, bars, rods, beams, profiles, channels, pipes, and other essential components.
Following the initial stages of steel production, a steel rolling mill employs two types of rolling processes to shape the hardened steel in its raw or semi-processed state into various forms:
• Hot Rolling;
• Cold Rolling.
During the hot rolling process, the steel is heated to extremely high temperatures until it reaches a red-hot state, and then it is rolled into the desired shape. In contrast, cold rolling involves rapidly cooling the steel and subjecting it to low temperatures to enhance its surface and mechanical properties.
Once the steel has undergone the cold rolling process, it becomes ready for practical use as a material. Whether it has undergone partial processing after hot rolling or complete processing after cold rolling, the steel is frequently coiled into large rolls for easy transportation and storage.
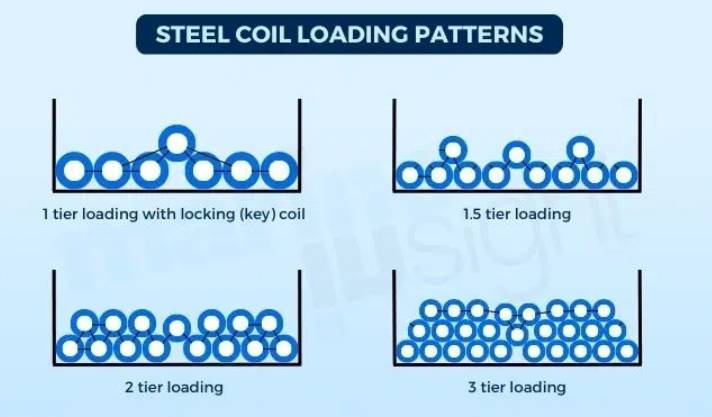
A hot-rolled coil refers to a coil of steel that is composed of hot-rolled or semi-processed steel. To be suitable for use, it requires additional treatment and cold-rolling. Hot-rolled steel coils are commonly subjected to annealing before being rolled. On the other hand, a cold-rolled coil is formed from steel that has undergone cold-hardening and rolling or complete processing.
Once again, these steel coils exhibit excellent surface and mechanical properties, making them ready for market use. Depending on the type of coil, they can be unwound for further processing or cold-rolling in the case of hot-rolled coils, or they can be fabricated into various products or items in the case of cold-rolled steel coils.
The majority of steel is transported in cargo vessels in the form of steel coils for logistical convenience. The shipping of steel coils constitutes a significant segment of the commercial freight market within the supply chain.
We are also acquainted with the sight of these large cylindrical coils being handled at cargo terminals and transported over land routes using trucks and trailers. However, there are specific regulations and guidelines that govern the appropriate stowage and transportation of these coils in significant quantities aboard ships.
Loading Steel Coils On Ships
These steel coils are typically transported in bulk and loaded into the designated cargo holds of the vessel. Each steel coil weighs approximately 40-50 tons, so certain measures must be taken before loading to ensure a smooth process:
- Inspecting the integrity and watertightness of the cargo holds, hatches, openings, ventilation systems, and loading cranage systems.
- Carefully inspecting the cargo holds and marking any sharp edges or points to ensure safety during handling.
- Ensuring the availability of loading and securing manuals along with a suitable loading plan. Although not specifically governed by a definitive framework, according to SOLAS VI regulations, securing manuals should be present for all types of cargo. Therefore, it is the responsibility of the operator and freight managers to ensure that the steel coils are stowed safely, securely, and efficiently, making optimal use of the available space.
The cargo holds must be thoroughly cleaned, washed with fresh water, and dried to remove any residual substances such as rust, debris, flakes, or other contaminants. Additionally, any remaining gases in the holds must be expelled. A “cleaning certificate” should be obtained from third-party providers to verify the cleanliness of the cargo holds, as required by regulations.
Loading and Unloading Procedure
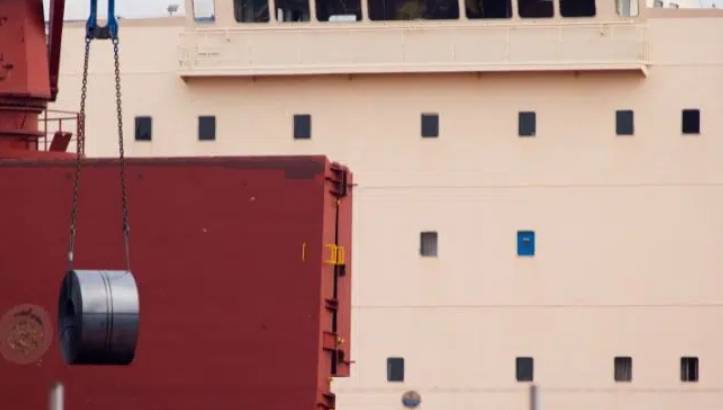
The loading process is conducted with great care using cranes and derricks, both on board the vessel and at cargo terminals or ports. The steel coils are usually lifted from their geometric center, utilizing braided steel wire wraps or slings as the suspension point. Tying chains are avoided to prevent any potential damage to the surface of the steel.
Great attention is given to preserving the integrity of the coils, particularly their surface condition (especially for cold-rolled and finished coils). Forklifts equipped with round or circular lifting section tines are employed instead of conventional rectangular ones with sharp edges. This precaution helps prevent any potential harm to the steel surfaces or distortion of the coil center during handling.
To ensure proper alignment, coils are consistently positioned in an axial orientation, with their circular centroid facing the fore-aft direction of the vessel. This alignment ensures optimal stability and secure stowage during transportation.
To prevent rolling motions and protect against damage, the coils are securely wedged at the bottom in a transverse direction. Wooden planks, also known as dunnages, are placed beneath the coils to provide sufficient friction and safeguard the steel surface. This arrangement ensures the coils remain stable and well-protected during transport.
Typically measuring around 25-30 mm in thickness, these dunnages serve as an intermediate layer between the coils and the ship’s plating. They play a crucial role in absorbing a considerable portion of the structural loads exerted by the coils, ensuring that these loads are evenly distributed across the vessel’s structure. This helps to prevent localized stress and potential damage to the ship during transportation.
Prior to their use, the dunnages undergo thorough drying to eliminate any moisture that could potentially lead to rusting or corrosion of the steel coils. Additionally, the securing wedges are firmly pinned in place to effectively prevent any movement of the coils during the voyage, thereby ensuring that dynamic loading is transferred to the vessel’s structure in a controlled manner. This meticulous process guarantees the safety and integrity of the cargo throughout the journey.
As per standard practice, the loading of coils is restricted to designated cargo holds and strictly prohibited on the deck or any other area above the strength deck. Careful consideration is given to optimize space utilization while avoiding abnormal or uneven distribution of the coils during the loading process. This approach ensures both safety and efficiency in the transportation of the cargo.
Additionally, the positioning of the dunnages is meticulously done to prevent the weight of the coils from being transferred to unsupported sections of the plating. This precautionary measure helps avoid localized static, dynamic, and fatigue loads. Instead, the weight of the coils is distributed along the bottom shell plating or inner bottom plating (in the case of double bottom vessels) as line-distributed loads. This distribution ensures that the maximum loading is primarily concentrated on the stiffening and deep members, which can better withstand the imposed forces.
However, this approach can pose challenges as it deviates from the loading information outlined in the cargo guidance manuals. It is important to note that steel coils are typically transported on large bulkers or general-purpose carriers that are specifically designed and reinforced to accommodate high load values. These vessels are equipped with sufficient strength and structural integrity to safely carry the steel coils, despite the variations in loading configurations.
Likewise, during the unloading process, the lashings and wedges are meticulously released, and the coils are systematically lifted using cranage equipment. The unloading sequence follows a similar pattern as the loading process, starting with the topmost layer and proceeding one coil at a time.
Stowage and Securing
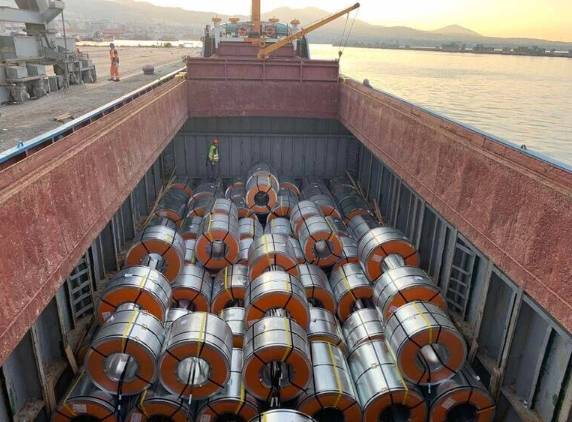
Once the steel coils are loaded, proper stowage and securing become crucial. Given the varying sizes and weights of the coils, the stowage principles are similar to other types of cargo. Typically, the coils are stowed in the lower holds and loaded from bottom to top, especially when dealing with a large quantity of coils.
To ensure that the center of gravity remains within acceptable limits, the heavier coils are loaded first and placed in the lower regions, while the lighter or smaller coils are placed on top. The coils are securely strapped or banded together using appropriate securing arrangements to prevent shifting or movement during transportation.
The steel coils are arranged athwartships in multiple tiers or levels, especially when a large number of coils are being transported. Each layer of coils is securely strapped to one another. When multiple rows of coils are stowed, a minimum clearance of 4 to 6 inches is maintained between the rows to prevent contact forces and potential damage during the loading and unloading processes.
A central coil, referred to as the key coil, is strategically selected at a central position both horizontally and vertically. Steel strappings are applied to secure this key coil to the adjacent coils as well as the coils positioned below it. This ensures stability and proper distribution of forces among the neighboring coils.
The strappings used are rigid metallic bands that are tightly tensioned, and in modern setups, pneumatic strappings are commonly employed. The key coil, when positioned on the bottom layer, is securely lashed and properly aligned.
The lower edge of the coil’s diameter is positioned at a distance below the top tip of the underlying coil, ensuring a gap of at least one-third of the latter’s geometric diameter. However, it should not exceed 60% of the diameter of the top or key coil.