The Brooklyn Bridge was inaugurated in May 1883 to great fanfare and a spectacular fireworks display. However, the truth is that the project had been in the works for 13 years, during which time several of the project’s leaders fell ill or died. Ultimately, it was the determination of a woman named Emily Warren Roebling that ensured the bridge’s completion.
When it was inaugurated, the Brooklyn Bridge was a remarkable feat of engineering, being the longest suspension bridge in the world. Its design, size and innovative use of steel in its construction made it an iconic landmark. Even after almost a century and a half, steel remains a crucial material in construction, industry, and many other facets of modern life.
The steel industry, key to decarbonization
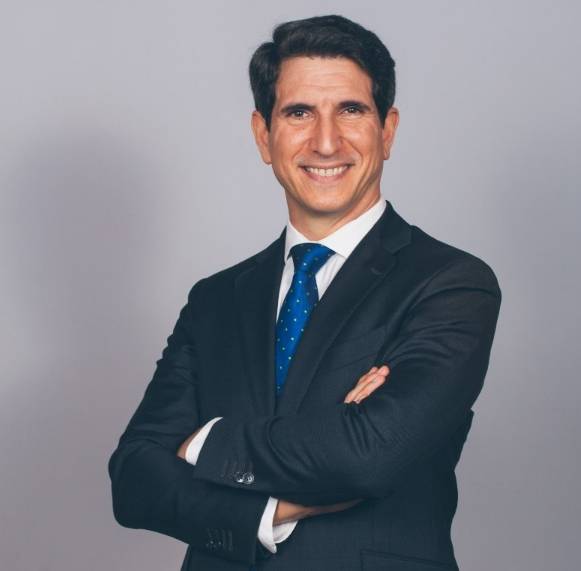
Javier Brey, President of the Spanish Hydrogen Association, emphasizes the significance of decarbonizing the steel industry for a more sustainable world. Steel is a ubiquitous material that we encounter in our everyday lives, from the structures of our homes to the electrical appliances we use, and even in our vehicles.
The World Steel Association reports that the steel sector provides direct employment to six million people. When considering indirect jobs, the figures show that the steel industry supports the employability of nearly 50 million people worldwide.
The rate of production in the steel industry has a considerable environmental impact. On average, 1.89 tons of carbon dioxide (CO2) are estimated to be emitted for every ton of steel produced, which contributes to between 7% and 9% of direct emissions from the global use of fossil fuels.
Brey explains that the steel sector is a crucial industry, but it is also one that emits a large amount of CO2. In Europe, for instance, the emissions associated with steel production account for 20% to 25% of the total emissions produced by the industry.
The steel industry is currently working on initiatives to develop technologies that further reduce the amount of CO2 emissions. While progress has been made since 1960, with a 60% reduction in energy consumption needed to produce each ton of steel, there is a climate urgency that requires more action.
Brey emphasizes that achieving sustainability is crucial in all aspects, including environmental, economic, political, technological, and business. He believes that the steel industry considers three essential factors: the cost of raw materials and energy, environmental regulations, and the interest in sustainability, as well as competition. Using green hydrogen as an energy source can help eliminate CO2 emissions, reduce costs, and compete against rising prices of fossil fuels.
And why green hydrogen?
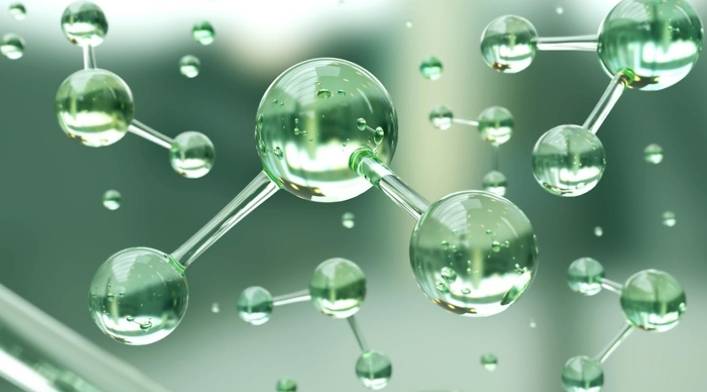
According to the Spanish Hydrogen Association, hydrogen is an energy carrier that can store energy and release it in a controlled manner. It can produce electrical or thermal energy with high efficiency and without emitting greenhouse gases such as CO2. The only byproduct of hydrogen combustion is water.
Green or sustainable hydrogen is produced through the water electrolysis process, which involves splitting water molecules into hydrogen and oxygen using electrical energy. This method is considered green when it is powered by renewable energy sources, and it has the advantage of emitting no greenhouse gases during production, making the entire hydrogen cycle clean.
The president of the Spanish Hydrogen Association explains that hydrogen offers the opportunity to store and manage renewable energy. During times of excess renewable energy, such as during the summer, the energy can be stored as hydrogen and utilized during periods of high demand when there is less renewable energy available, such as in autumn and winter. This means that hydrogen allows for the extensive and prolonged management of renewable energy.
Applications in the steel sector
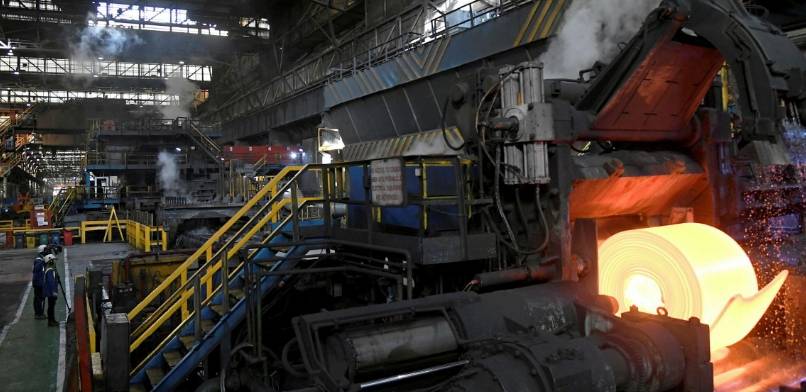
The steel sector employs hydrogen as an energy source in two main ways. The first application is related to its capacity to produce high temperatures. In steel production, blast furnaces burn fuels to achieve these high temperatures.
According to the World Steel Association, temperatures as high as 17,000 °C are required in steel production. This is hotter than lava.
“If traditional fuels such as coal are replaced with green hydrogen, these high temperatures can be achieved without emitting CO2,” says the expert.
Another potential application of hydrogen in the steel sector is its use as a reductant. Steel production requires a reducing atmosphere that lacks oxygen and has specific chemical conditions. In the past, using hydrogen as a reductant was expensive, so other more polluting alternatives such as natural gas were used. However, the possibility of using hydrogen as a reductant now presents an opportunity to reduce CO2 emissions, according to Brey.
Two main challenges need to be addressed to make green hydrogen a key component in steelmaking: establishing production and transport infrastructure, and bringing about change within the sector itself. According to the president of the Spanish Hydrogen Association, modifications must be made to blast furnaces and other processes in order to integrate green hydrogen. Although the technology exists, implementation will require time.
The transformation of the steel sector towards green hydrogen would require innovation and digitization. According to María Mendiluce, CEO of the We Mean Business coalition, a non-profit organization that works with influential companies to reduce polluting emissions,
“Digitization plays a crucial role in the optimal utilization of resources. For instance, a company in Sweden has produced the first ton of steel with zero emissions using hydrogen. With the help of the government, the producing company, and Volvo, which has demanded this material, the steel without emissions that was expected to be produced in 2040 can now be achieved by 2033. This disruption was carried out in one plant and can be replicated effectively throughout the world.”
The green hydrogen map
At present, seven significant projects in France, Sweden, and Germany are dedicated to incorporating green hydrogen into the steel industry. Moreover, there is a growing interest from major players, industries, and companies that prioritize reducing their carbon footprint in their short and medium-term plans.
Notable names in this effort include Liberty Steel Group, H2 Green Steel, SSAB, and AcerlorMittal.
“Projects like these will demonstrate the feasibility and profitability of producing steel from renewable sources,” says Brey.
Work is also being carried out in Spain to launch the first such projects, which could eventually lead to self-sufficiency.
Javier Brey concludes that as many industries and companies are striving to reduce their carbon footprint, they will demand similar reductions from steel manufacturers. The price of production will be a key factor, and the existing environmental regulations and commitments will also play a role, as previously mentioned.